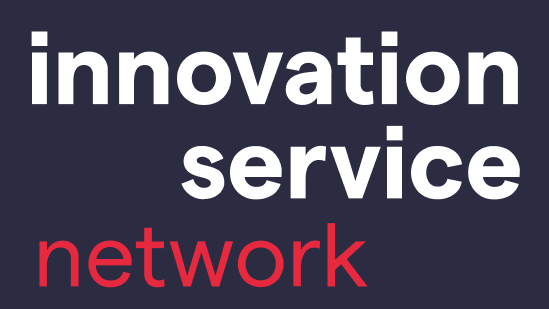
Quick Links
Menu
Quick Links
Menu
The counseling was carried out in two parts: training of employees to work with the FMEA method - 4th edition and introduction of the method with the help of a concrete case from the company. Employees in the field of design and technology, quality assurance and production learned about the FMEA method, were trained to work with the 4th edition and also learned about computer support in performing the analysis. They took into account the advice given and used the acquired knowledge to meet the requirements of the customer (Magna), who conditioned the contractual cooperation with the company with the support process of FMEA analysis and requested analysis for the product fuel filler carrier.
Workshop and training participants learned about the method and were trained to introduce the method into business processes. The use of FMEA - 4th edition was also requested by buyers from the automotive segment. Therefore, based on the introduction of this method, the company retained existing customers and gained additional market share in foreign markets (Blau, Magna), and above all, based on consulting in the preparation of analysis for a specific product, obtained confirmation of the offer.
The area of consulting was Time Management in Production Processes. Thus, the training of two time analysts in the company was carried out, who were then the contractors and administrators of the system of determining normative times for work operations. Thus, they learned how to set norms and especially chronometry. The emphasis of the consulting was also on identifying and eliminating organizational losses in the company that significantly affect the realization of delivery times, efficient production planning, realistic calculation of costs - own prices for bids and to motivate employees in rewarding.
Two employees were trained to determine normative times and analyze organizational losses.
The timing of the assembly on the spot welding machine was performed, and on the basis of the recorded losses with the MTO method, the optimization of the production process and job design was performed. Management and control of production times is one of the necessary conditions for achieving competitive advantage, so the company attaches great importance to this discipline.
Together with experienced innovation managers, your ideas will become reality! We look forward to working together!